A machinery system has been designed to palletize bags of animal feed from a bag conveyor line to a pallet conveyor line. This machinery includes a pallet dispenser, a slip sheet applicator, as well as wrapping stations. The system is designed to transfer the bags quickly and efficiently to the wrapping station, allowing for efficient and effective palletizing of the animal feed.
An industrial robot is equipped with a custom gripper that can pick up and place bags onto a wooden pallet. This pallet is supported by one segment of a total of five conveyors, each of which can be individually controlled. This allows for greater flexibility and control when it comes to the placement of the bags. The robot’s gripper is designed to make the process of picking and placing the bags on the pallet easier and more efficient.
In order to increase safety, three safety zones were implemented. These zones were designed to create a safe environment for the operator to interact with the machine.
Key Information:
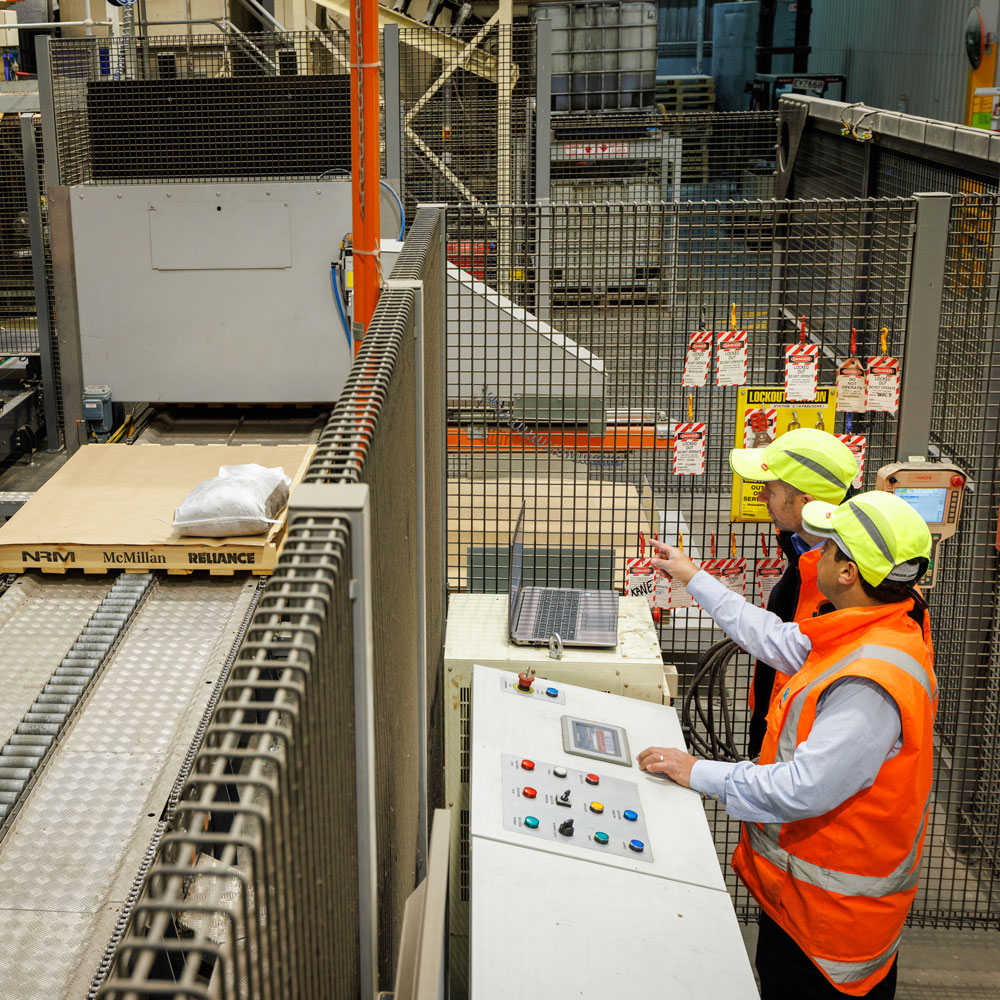
Project Summary
- Design and procure the electrical and automation items that comply with Safety Performance Level D (PLd). Design the electrical and Automation drawings using Eplan software.
- Design the electrical and automation drawings using Eplan software.
- Programming the integrated PLC/ Safety PLC, Fieldbus network, HMI and configuring the VFDs, instruments, and the safety guards will be done based on the PackML unit/machine implementation standards.
- Conducting of the Functional Acceptance Test (FAT)
- Install the switchboards and the safety gear on site.
- Commissioning and start-up.
- Ongoing support as needed.
Complexity Managed
The Palletizing machinery with Safety Performance Level d (PLd) was a complex system requiring precise integration between its safety and operations components. The interface between the robot and the Safety PLC was particularly challenging as it was crucial for the system to function correctly. The successful integration of these two components required a great deal of effort, and it is commendable that the machinery is now running optimally.
Project Outcome
Farmlands were very delighted with the projects and services provided by our team. We are proud to have met their expectations.
The line has permanently increased efficiency, safety and output. Millennium worked with the robot supplier to integrate a palletizing robot and automate a variety of equipment, making the entire line more efficient.