Millennium Electrical was engaged to design an electrical and industrial automation solution for a palletising system.
The system operates by feeding bags into three individually controlled conveyors that rotate, prepare, and stage the bags for picking by a robot (supplied by a third party). The robot is equipped with a custom gripper to place the bags on wooden pallets, which are supported by one of five individually controlled conveyors.
A Scott PHS pallet dispenser loads pallets onto the pallet conveyor, while a Scott PHS slip sheet dispenser applies a slip sheet prior to stacking. Full pallets are conveyed to a manually operated pallet wrapper. Downstream pallet conveyors act as a buffer, holding up to four full pallets when the wrapper is full or not in use.
Millennium Electrical selected Safety PLC, HMI, and VSD, and electrical components from Rockwell Automation to meet Performance Level D (PLC) safety standards. Our control system engineer configured the safety controller, fieldbus network, and software, while also handling integration with the robot. Our electricians installed and configured the safety guards and field devices.
Key Information:
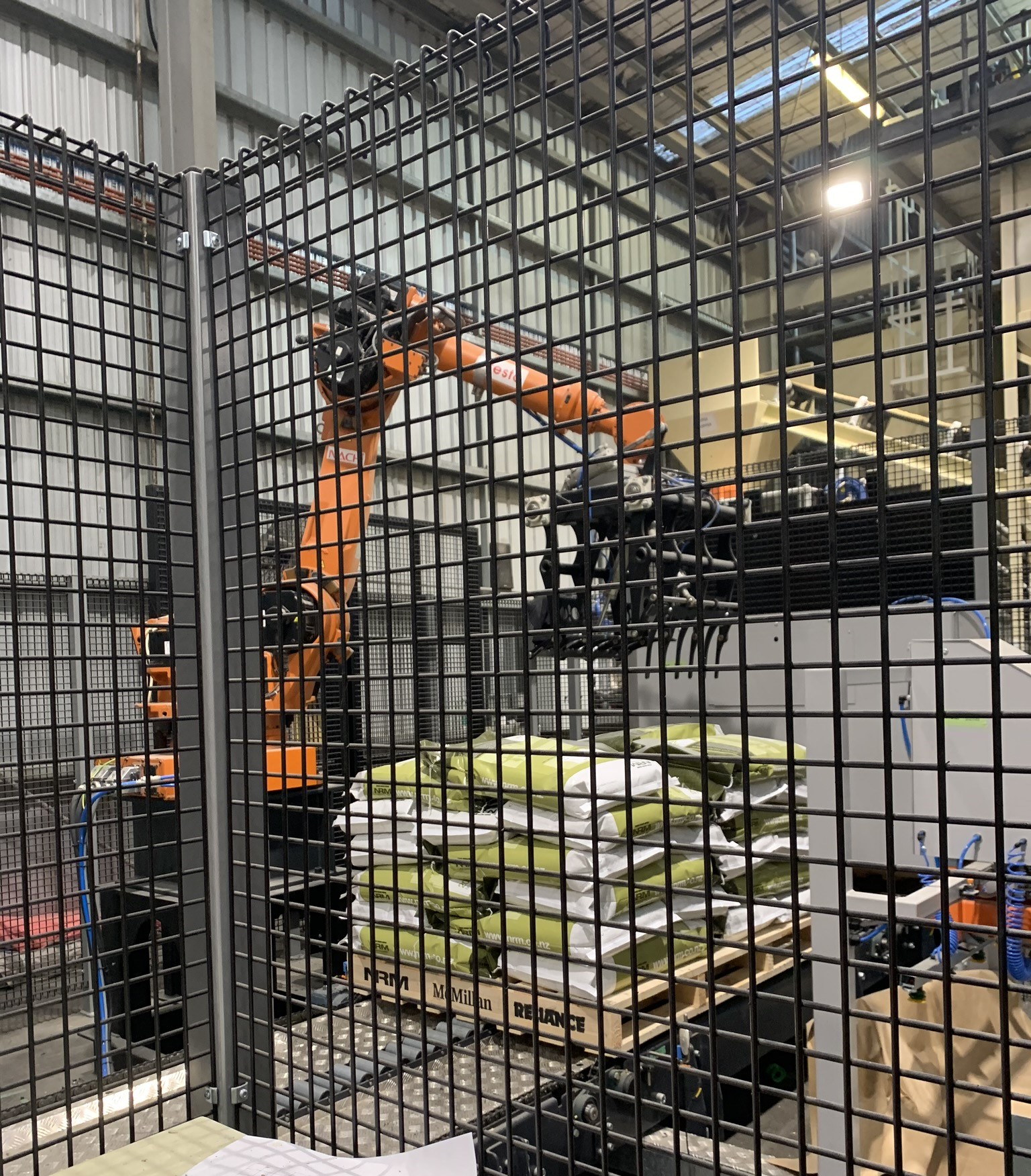
Project Size
- Five Engineers from the Main Contractor Side
- Two Engineers and Two Electricians from Millennium Team
- Production maintains a rate better than 8 seconds per bag, plus pallet conveying time
- Three product types are handled, with stacking patterns ranging from 40 to 80 bags per pallet
Project Outcomes
We have successfully conducted a factory acceptance test, followed by the site installation, commissioning and post commissioning services.
The client was very pleased with the quality of work and deliverables, which led to long time business relationship.